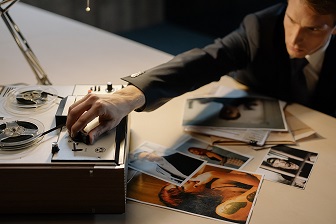
Pharma investigations
Investigations in the pharmaceutical industry are critical for identifying and addressing issues that may affect the safety and quality of products, as well as compliance with regulatory standards. A well-conducted investigation can help to determine the root cause of a problem and implement corrective and preventive actions (CAPAs) to prevent it from happening again. Here are some common tools used in the investigation process and examples of how they can be applied:
- Ishikawa diagram (also known as a fishbone or cause-and-effect diagram): This tool is used to identify the potential causes of a problem. For example, if a batch of medication is found to be contaminated, an Ishikawa diagram can be created to identify the potential causes, such as the raw materials used, the manufacturing process, or the storage conditions.
- Personnel interviews: Interviews with personnel involved in the process can provide valuable information about the problem and its potential causes. For example, if a batch of medication is found to be contaminated, personnel who were involved in the manufacturing process can be interviewed to determine if there were any deviations from standard operating procedures.
- Brainstorming: Brainstorming sessions bring together a diverse group of individuals to generate ideas and identify possible causes of a problem. For example, if a batch of medication is found to be contaminated, a brainstorming session can be held to identify all possible causes, including those that may not have been considered before.
- Why-Why Analysis: This tool helps to identify the root cause of a problem by asking “why” questions. For example, if a batch of medication is found to be contaminated, a why-why analysis can be conducted to determine why the contamination occurred and what actions can be taken to prevent it from happening again.
- Go to Gamba: This is a process of going directly to the area where the problem occurred to observe and collect information. For example, if a batch of medication is found to be contaminated, a team can go to the manufacturing facility to observe the process and collect additional information.
- Why why Analysis : Why why analysis also sometimes referred as 5 why analysis is a tool to continuously ask why till you get the exact root cause. This is usually limited to 5 whys. This helps in eliminating the other factors which are not responsible for the happening.
- Getting the exact root cause: Once potential causes have been identified, it is important to confirm the root cause by gathering additional data and information. For example, if a batch of medication is found to be contaminated, additional tests can be conducted to confirm the root cause of the contamination.
- CAPAs: Based on the root cause, corrective and preventive actions should be taken to prevent the problem from happening again. CAPAs taken should be robust enough to eradicate the problem from root. For example, if a batch of medication is found to be contaminated due to a deviation from standard operating procedures, a CAPA can be implemented to ensure that the deviation is not repeated in the future.
In conclusion, conducting investigations in the pharmaceutical industry is crucial for ensuring the safety and quality of products and compliance with regulatory standards. By using tools like Ishikawa diagrams, personnel interviews, brainstorming, why-why analysis, go to gamba, getting the exact root cause, and taking CAPAs based on the root cause, organizations can effectively identify and resolve problems and improve their processes.