Cleaning validation is a critical process in the pharmaceutical industry that ensures that manufacturing equipment and facilities are clean and free of contaminants. The cleaning validation process is designed to prevent cross-contamination, which can compromise the quality and safety of pharmaceutical products.
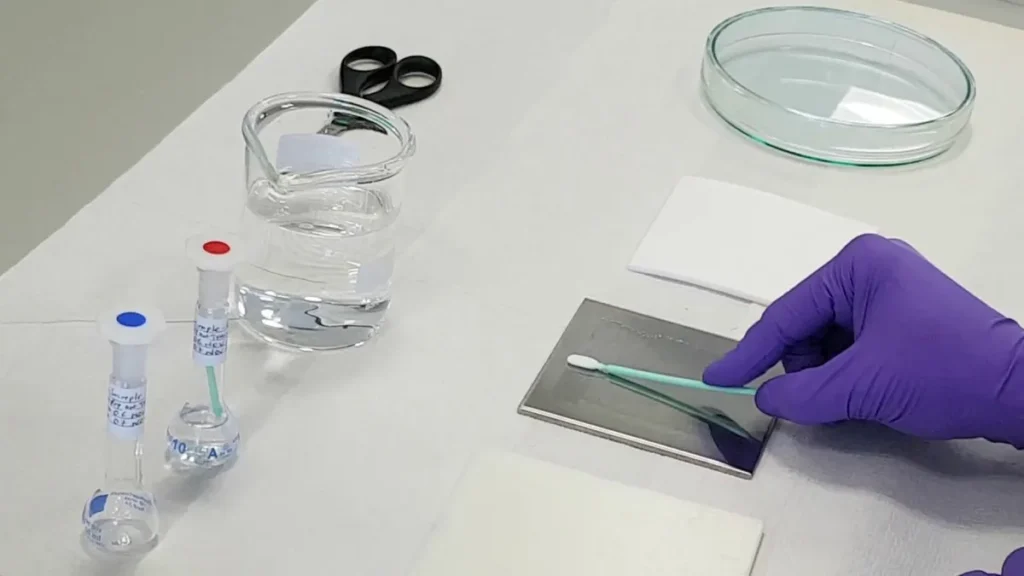
The cleaning validation process is typically based on guidelines from organizations such as the Active Pharmaceutical Ingredients Committee (APIC) and regulatory agencies such as the US Food and Drug Administration (FDA) and the European Medicines Agency (EMA).
One important aspect of cleaning validation is determining the maximum allowable carryover (MACO) of residual active pharmaceutical ingredients (APIs) and other contaminants from previous batches. This MACO calculation takes into account factors such as the toxicity data, Therapeutic Daily Dose(TDD) and permitted daily exposure (PDE) limits for the specific API.
The MACO is then used to set acceptance criteria for swab and rinse samples taken from the equipment after cleaning. Swab samples are taken from specific areas of the equipment, while rinse samples are taken from the entire surface area of the equipment. Both types of samples are analyzed for residual levels of the API and other contaminants.
The equipment chain is an important consideration in cleaning validation. This includes all equipment, such as pumps, valves, and transfer lines, that comes into contact with the product. The equipment chain must be considered as a whole, and the cleaning validation process must ensure that all areas of the equipment chain are effectively cleaned.
The use of validated cleaning agents, cleaning procedures, and equipment is essential in the cleaning validation process. The cleaning agents must be effective in removing the specific residues, and the cleaning procedures must be validated to ensure that they are effective in removing residues from all areas of the equipment. The equipment used in the cleaning process must also be validated to ensure that it does not contribute to contamination.
Rinse and swab sampling methods are critical to the cleaning validation process. Rinse samples are taken after the equipment has been cleaned and rinsed with water or another cleaning agent. Swab samples are taken by rubbing a sterile swab over a specific area of the equipment. The samples are then analyzed to determine if the equipment is clean and if the cleaning process is effective.
In conclusion, cleaning validation is a complex process that involves careful planning, execution, and documentation. It requires consideration of factors such as MACO calculations, swab and rinse sampling methods, equipment chain, and validated cleaning agents and procedures. By following guidelines such as those from APIC and regulatory agencies, pharmaceutical companies can ensure that their equipment and facilities are clean and free of contaminants, resulting in safe and high-quality pharmaceutical products.