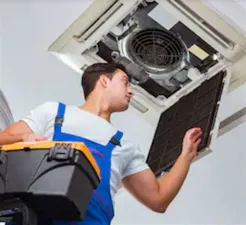
This articles briefly explains the qualification/ validation of HVAC/AHU !!
Basics of HVAC/AHU :
Heating, ventilation, and air conditioning (HVAC) systems play a crucial role in the pharmaceutical industry. These systems are responsible for maintaining the required environmental conditions that are necessary for the manufacture, testing, and storage of pharmaceutical products. The validation of HVAC systems is therefore critical to ensure that the systems are functioning as per the required specifications and standards.
Validation of HVAC systems in the pharmaceutical industry is essential to ensure that the systems are performing as per the design requirements. The validation process involves testing and documentation of the HVAC system performance. The main objective of the validation process is to ensure that the HVAC system is capable of maintaining the required environmental conditions throughout the pharmaceutical manufacturing process.
The validation process typically involves three stages: Installation Qualification (IQ), Operational Qualification (OQ), and Performance Qualification (PQ). In the IQ stage, the HVAC system is installed and tested to ensure that it meets the design specifications. The OQ stage involves testing the system under various operational conditions to ensure that it performs as per the design requirements. The PQ stage involves testing the system under actual operating conditions to ensure that it meets the requirements of the pharmaceutical manufacturing process.
Validation of HVAC systems in the pharmaceutical industry involves several parameters such as temperature, humidity, air velocity, and pressure. The temperature and humidity levels should be maintained within a specified range to prevent degradation of pharmaceutical products. The air velocity should be sufficient to prevent the accumulation of contaminants, while the pressure should be controlled to prevent cross-contamination between different areas.
The validation process also involves the testing of the HVAC system’s filters to ensure that they are effective in removing contaminants from the air. The filters should be tested for their efficiency in removing particles of different sizes, including bacteria and viruses.
Documentation plays a crucial role in the validation process of HVAC systems in the pharmaceutical industry. All test results and procedures should be recorded and documented for future reference. The documentation should also include details of the HVAC system design, installation, and maintenance procedures.
Guidelines to follow for HVAC/AHU qualification:
International Society for Pharmaceutical Engineering (ISPE) – This organization provides guidance on the design, construction, and qualification of HVAC systems for pharmaceutical facilities.
American Society of Heating, Refrigerating, and Air-Conditioning Engineers (ASHRAE) – This organization provides guidance on the design and operation of HVAC systems for cleanrooms and other controlled environments.
European Commission – The European Commission provides guidelines on the design, installation, and operation of HVAC systems for pharmaceutical facilities in the European Union.
World Health Organization (WHO) – The WHO provides guidelines on the design, installation, and operation of HVAC systems for pharmaceutical facilities in developing countries.
Above guidelines are essential for the qualification and operation of HVAC systems in the pharmaceutical industry. These guidelines ensure that HVAC systems meet the required standards for product quality, safety, and efficacy.
However, ISO14644 guideline helps in a more detailed way as follows:
ISO 14644 is a series of standards developed by the International Organization for Standardization (ISO) that provides guidance on the classification of air cleanliness in cleanrooms and controlled environments. The ISO 14644 standards are used globally by various industries, including pharmaceuticals, microelectronics, and healthcare, to ensure that the air quality in cleanrooms and controlled environments meets the required standards.
ISO 14644-1 provides guidelines for the classification of air cleanliness in cleanrooms and controlled environments based on the number and size of particles in the air. The standard specifies the maximum allowable concentration of particles in the air based on the particle size and the class of cleanroom. The classes range from ISO Class 1 (fewest particles) to ISO Class 9 (most particles).
ISO 14644-2 provides guidelines for the monitoring of cleanrooms and controlled environments to ensure that they meet the required air cleanliness standards. The standard specifies the methods for sampling and measuring particles in the air and the frequency of monitoring required based on the class of cleanroom.
ISO 14644-3 provides guidelines for the testing and certification of cleanrooms and controlled environments to ensure that they meet the required air cleanliness standards. The standard specifies the methods for testing the performance of cleanroom systems, including air supply, air distribution, and air exchange rates.
HVAC/AHU Qualification tests:
1.Filter Integrity Tests: Filter integrity tests verify the effectiveness of the HVAC system filters in removing contaminants from the air. The test involves the use of a particle counter to measure the particle count before and after the filter. A differential pressure gauge measures the pressure differential across the filter, and a leak test is performed to verify that the filter does not have any leaks.
2. Viable particle count: It is a critical parameter in the pharmaceutical industry to ensure product quality and safety. Air classification standards, such as ISO 14644-1, define acceptable limits for viable particle counts in different cleanroom classifications. Instruments used to measure viable particle counts include air samplers and microbial impaction devices. Air samplers use a vacuum to draw air through a collection medium, while microbial impaction devices use a plate with a nutrient medium to capture viable particles. Regular monitoring and maintenance of the HVAC/AHU system, including air filtration systems such as HEPA filters, is necessary to ensure that the viable particle count remains within acceptable limits.
3. Non-viable particle count refers to the number of non-living particles present in the air, such as dust, fibers, and other airborne contaminants.Non-viable particle counts are measured separately from viable particle counts and are also subject to acceptable limits defined by air classification standards such as ISO 14644-1. Airborne non-viable particles can be generated from various sources, including people, equipment, and processes. Regular monitoring and maintenance of the HVAC/AHU system and air filtration systems are necessary to control non-viable particle counts and ensure product quality and safety. Instruments used to measure non-viable particle counts include particle counters, which use a laser to detect and count particles in a given volume of air.
4. Smoke Tests: Smoke tests verify the airflow patterns of the HVAC system. The test involves the use of smoke generators to introduce smoke into the HVAC system. The smoke is then tracked to verify the airflow patterns and ensure that the system is providing adequate air movement.
5. Area Recovery Tests: Area recovery tests verify that the HVAC system can quickly recover from a power outage or system shutdown. The test involves shutting down the HVAC system and measuring the time required for the system to recover and return to normal operation. This test is critical to ensure that pharmaceutical products are not affected by any downtime in the HVAC system.
6.Temperature and Humidity Tests: Temperature and humidity tests verify that the HVAC system is maintaining th e required temperature and humidity levels in the manufacturing area. The test involves the placement of temperature and humidity sensors at various locations in the manufacturing area to monitor the temperature and humidity distribution.
7. Air Velocity Tests: Air velocity tests verify that the HVAC system is providing adequate air movement in the manufacturing area to prevent the accumulation of contaminants. The test involves the use of an anemometer to measure the air velocity at various locations in the manufacturing area.
8. ACPH Tests: ACPH (Air Changes per Hour) tests verify that the HVAC system is providing the required number of air changes per hour in the manufacturing area. The test involves the use of a tracer gas to measure the time required for the HVAC system to remove a specified percentage of the tracer gas from the manufacturing area.
9. Pressure Differential Tests: Pressure differential tests ensure that the HVAC system is maintaining the required pressure differential between different areas in the manufacturing facility to prevent cross-contamination. The test involves the use of pressure gauges to measure the pressure differential between various areas in the manufacturing facility.
In conclusion, the validation of HVAC systems in the pharmaceutical industry is critical to ensure that the systems are functioning as per the required specifications and standards. The validation process involves testing and documentation of the HVAC system performance, and it should be conducted in accordance with industry standards and guidelines. Proper validation of HVAC systems can prevent contamination of pharmaceutical products, ensure product quality, and protect the health and safety of the users.