
Out of Specification (OOS) and Out of Trend (OOT) guideline was published by MHRA (Medicines and Healthcare Products Regulatory Agency in October 2017 which is complementary to FDA guidance on investigating OOS Test results in Pharmaceutical Production October 2006.
Investigations of “Out of Specification (OOS) / Out of Trend (OOT)/ Atypical results” have to be done in cases of:
-Batch release testing and testing of starting materials.
-In-Process Control testing: if data is used for batch calculations/decisions and if in a dossier and on Certificates of Analysis.
-Stability studies on marketed batches of finished products and or active pharmaceutical ingredients, on-going / follow up stability (no stress tests)
-Previous released batch used as reference sample in an OOS investigation showing OOS or suspect results.
-Batches for clinical trials.
Out of Specification (OOS) and Out of Trend (OOT) results necessitate a thorough investigation process in the pharmaceutical industry to ensure product quality and safety. These investigations are divided into 3 distinct phases: Phase Ia, Phase Ib, Phase II, and Phase III. Each phase has specific objectives and processes to identify the root cause of deviations and implement corrective actions.
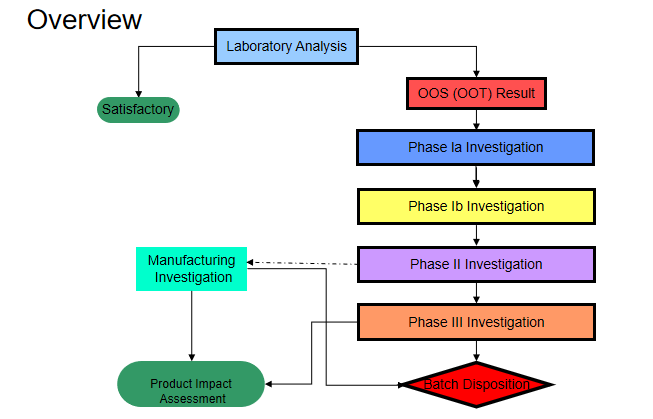
Phase Ia – Laboratory Investigation: Initial Analysis
Objective: The primary goal is to identify any obvious laboratory errors that might have led to the OOS or OOT results.
Process:
- Initial Review by Analyst:
- Immediate assessment of the test procedure, calculations, and raw data for apparent errors.
- Identification of obvious errors like incorrect sample preparations or instrument malfunctions.
- Documentation:
- Detailed documentation of all findings and corrective actions taken.
Outcome: If an obvious error is found, corrective actions are implemented, and no further investigation is needed. If not, the process moves to Phase Ib.
Flow Diagram:
Initial Review by Analyst -> Identify Obvious Errors? -> Yes -> Implement Corrective Actions| If No | Proceed to Phase Ib
Phase Ib – Laboratory Investigation: In-Depth Analysis
Objective: To conduct a detailed investigation to identify less apparent laboratory errors.
Process:
- Hypothesis Testing:
- Detailed examination of the test environment, reagent quality, and analyst competency.
- Use of a laboratory investigation checklist to ensure all possible errors are considered.
- Additional Testing:
- Retesting the sample, if necessary, to verify the results.
- Conducting parallel testing with control samples.
- Documentation:
- Recording all findings and actions taken during the investigation.
Outcome: If no assignable cause is found, the investigation proceeds to Phase II.
Flow Diagram:
Detailed Examination -> Retesting Required? -> Yes -> Conduct Retesting -> Document Results| If No | Proceed to Phase II
Phase II – Manufacturing Investigation
Objective: To identify any manufacturing process errors that could explain the OOS or OOT results.
Process:
- Review of Production Records:
- Examination of batch records, production logs, and environmental monitoring data.
- Verification of raw material quality, equipment calibration, and adherence to SOPs.
- Hypothesis Testing:
- Identification of potential root causes related to the manufacturing environment.
- Testing and validation to confirm or refute the hypothesized causes.
- Corrective and Preventive Actions (CAPA):
- Implementation of measures to correct identified issues and prevent recurrence.
- Documentation of all findings, actions, and final conclusions.
Outcome: Identification of manufacturing process errors and implementation of CAPA.
Flow Diagram:
Review Production Records -> Identify Potential Root Causes? -> Yes -> Test and Validate Causes -> Implement CAPA -> Document Results | If No | Document Findings
Phase III – Full-Scale Investigation
Objective: To conduct a comprehensive investigation involving all relevant departments to resolve persistent or critical OOS/OOT issues.
Process:
- Cross-Functional Team Involvement:
- Collaboration between production, quality assurance, engineering, and other relevant departments.
- Systematic Investigation:
- Detailed examination of the entire production and quality control process.
- Identification of systemic issues affecting multiple batches or products.
- Implementation of Systemic CAPA:
- Development and implementation of long-term corrective actions.
- Monitoring and verification of the effectiveness of CAPA.
Outcome: Resolution of complex OOS/OOT issues and enhancement of overall quality systems.
Flow Diagram:
Cross-Functional Team Meeting -> Conduct Systematic Investigation -> Identify Systemic Issues? -> Yes -> Develop and Implement Systemic CAPA -> Monitor Effectiveness -> End | If No | Document Findings
Conclusion
Each phase in the OOS and OOT investigation process serves a critical function, from identifying laboratory errors to uncovering manufacturing issues and implementing systemic corrective actions. By following these structured phases, pharmaceutical companies can ensure the quality and safety of their products, comply with regulatory standards, and maintain the integrity of their manufacturing processes. Explore the comprehensive phases of Out of Specification (OOS) and Out of Trend (OOT) investigations in pharmaceuticals. Learn about Phase Ia, Phase Ib, Phase II, and Phase III investigations, their processes, objectives, and outcomes. Ensure pharmaceutical quality assurance and regulatory compliance through structured investigations and effective Corrective and Preventive Actions (CAPA).
Reference links : https://mhrainspectorate.blog.gov.uk/2018/03/02/out-of-specification-guidance/
Ümraniye hızlı süpürge servisi Üst düzey bir tamir deneyimi sundular. http://domainrama.com/read-blog/5298
Here, you can access a great variety of slot machines from top providers.
Users can experience retro-style games as well as modern video slots with stunning graphics and bonus rounds.
Whether you’re a beginner or a seasoned gamer, there’s something for everyone.
casino
The games are instantly accessible anytime and optimized for desktop computers and smartphones alike.
No download is required, so you can jump into the action right away.
Platform layout is easy to use, making it quick to explore new games.
Register now, and enjoy the thrill of casino games!
Here, you can discover a great variety of slot machines from famous studios.
Players can experience classic slots as well as modern video slots with vivid animation and bonus rounds.
Whether you’re a beginner or a casino enthusiast, there’s something for everyone.
slot casino
The games are ready to play round the clock and optimized for desktop computers and smartphones alike.
No download is required, so you can start playing instantly.
Platform layout is easy to use, making it quick to explore new games.
Join the fun, and enjoy the excitement of spinning reels!
This website, you can find lots of casino slots from top providers.
Users can enjoy retro-style games as well as feature-packed games with stunning graphics and interactive gameplay.
Even if you’re new or an experienced player, there’s always a slot to match your mood.
play aviator
Each title are ready to play round the clock and optimized for laptops and smartphones alike.
All games run in your browser, so you can jump into the action right away.
The interface is user-friendly, making it quick to explore new games.
Sign up today, and dive into the excitement of spinning reels!
At this page, you can discover different websites for CS:GO betting.
We offer a wide range of wagering platforms centered around Counter-Strike: Global Offensive.
Each site is thoroughly reviewed to ensure safety.
csgo skin betting sites
Whether you’re a seasoned bettor, you’ll conveniently choose a platform that suits your needs.
Our goal is to guide you to access reliable CS:GO gaming options.
Check out our list today and upgrade your CS:GO gambling experience!
On this platform, you can access a great variety of online slots from leading developers.
Visitors can experience traditional machines as well as feature-packed games with stunning graphics and bonus rounds.
If you’re just starting out or a seasoned gamer, there’s always a slot to match your mood.
slot casino
All slot machines are ready to play 24/7 and optimized for desktop computers and mobile devices alike.
No download is required, so you can start playing instantly.
Platform layout is user-friendly, making it quick to browse the collection.
Join the fun, and enjoy the thrill of casino games!
Searching for someone to take on a one-time hazardous task?
This platform focuses on connecting customers with workers who are ready to execute high-stakes jobs.
Whether you’re handling urgent repairs, unsafe cleanups, or complex installations, you’ve come to the perfect place.
Every listed professional is pre-screened and qualified to guarantee your security.
hitman for hire
This service offer transparent pricing, detailed profiles, and safe payment methods.
No matter how difficult the scenario, our network has the expertise to get it done.
Begin your quest today and locate the ideal candidate for your needs.
The platform offers valuable information about methods for becoming a hacker.
Content is delivered in a simple and understandable manner.
One can grasp numerous approaches for accessing restricted areas.
Additionally, there are practical examples that exhibit how to implement these skills.
how to learn hacking
Complete data is regularly updated to align with the recent advancements in information security.
Special attention is centered around applied practice of the learned skills.
Take into account that every procedure should be used legally and through ethical means only.
This website features various medications for ordering online.
Users can conveniently buy health products without leaving home.
Our range includes both common solutions and more specific prescriptions.
Everything is sourced from verified pharmacies.
how long does cialis take to work
We ensure quality and care, with secure payments and fast shipping.
Whether you’re filling a prescription, you’ll find affordable choices here.
Explore our selection today and experience convenient support.
Our platform offers a large selection of prescription drugs for easy access.
Anyone can securely buy treatments without leaving home.
Our inventory includes popular drugs and custom orders.
Each item is provided by reliable pharmacies.
order kamagra
Our focus is on customer safety, with secure payments and on-time dispatch.
Whether you’re managing a chronic condition, you’ll find trusted options here.
Begin shopping today and experience convenient access to medicine.
Here, access interactive video sessions.
Interested in casual conversations business discussions, this platform has something for everyone.
This interactive tool developed to foster interaction from around the world.
With high-quality video along with sharp sound, each interaction feels natural.
Participate in open chat spaces connect individually, depending on your preferences.
https://rt.ruletka-chat.com/
All you need consistent online access plus any compatible tool to get started.
Mechanical watches remain the epitome of timeless elegance.
In a world full of digital gadgets, they still hold their charm.
Built with precision and mastery, these timepieces showcase true horological mastery.
Unlike fleeting trends, manual watches do not go out of fashion.
https://trackrecord.id/read-blog/10738
They stand for heritage, tradition, and enduring quality.
Whether worn daily or saved for special occasions, they forever remain in style.
More than ever
shoppers opt for
digital purchases. Starting with fashion
to furniture, practically all items
can be bought without leaving your house.
The rise of digital shopping redefined
retail experiences.
https://superlooks.ru/look/58-new-balance-500-universalnye-krossovki-dlya-bolshogo-goroda/
This is a very detailed and informative overview of the OOS and OOT investigation process in the pharmaceutical industry. It’s impressive how structured and systematic the approach is, ensuring both product quality and regulatory compliance. I particularly appreciate the emphasis on identifying root causes and implementing corrective actions, as this is crucial for long-term improvements. However, I wonder how often these phases lead to significant changes in manufacturing processes or if they mostly address isolated incidents. Do you think the current framework is sufficient to handle emerging challenges in the industry, such as advanced biologics or personalized medicines? It would be interesting to hear your thoughts on whether these phases need to evolve with the industry’s advancements.